Solar Heater Manufacturing Plant From Start to Finish
We follow a streamlined and precise process to manufacture high-quality canisters that meet global standards. Solar Heater Manufacturing Plant in India, in each step in our process is designed to ensure durability, efficiency, and superior craftsmanship.
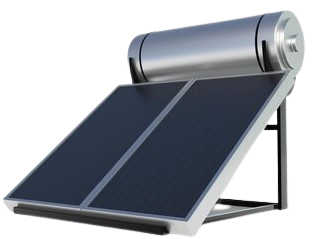
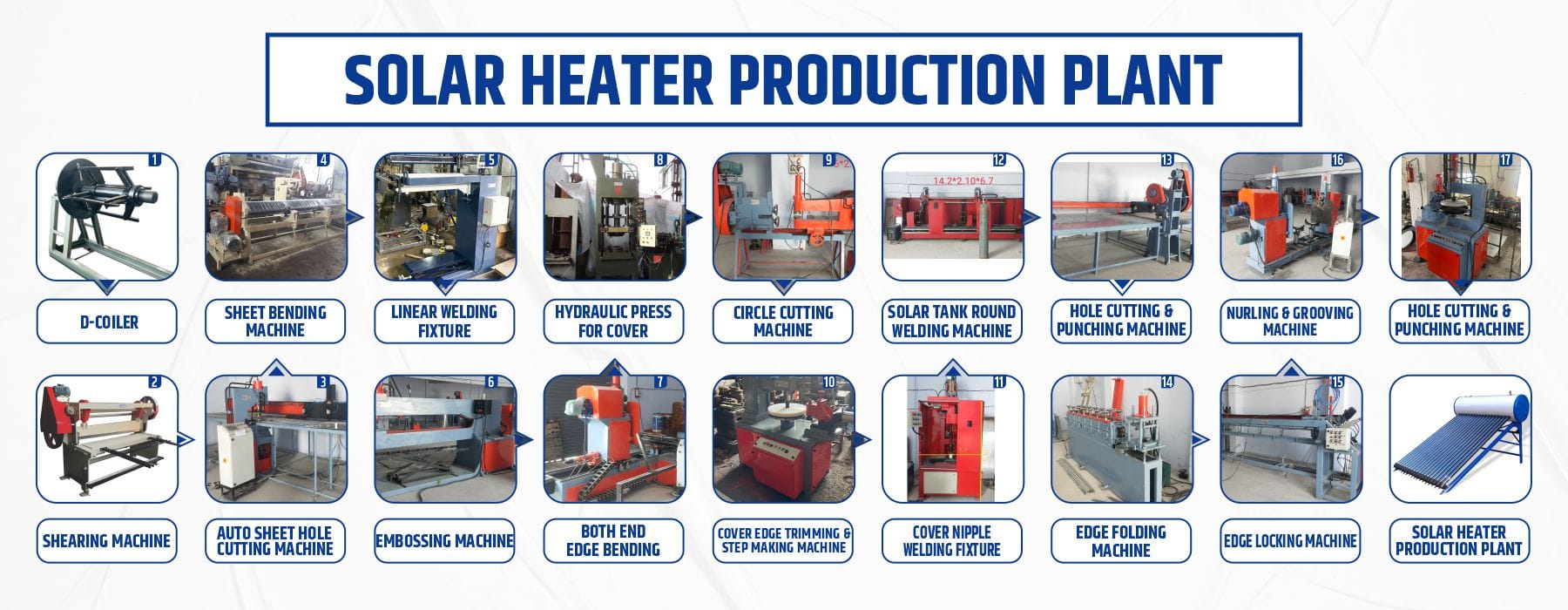
The D-Coiler holds and unrolls the metal sheet for processing. It ensures a steady and controlled feed into the next machine. This step prevents material wastage and enhances efficiency.
Shearing Machine
The sheet is cut to precise dimensions as per requirements. Accurate cutting ensures proper fitment of parts. This step is crucial for maintaining uniformity in production.
Learn More
Automated hole cutting ensures precise and evenly spaced perforations. It enhances the structural integrity of the solar heater components. This step speeds up the production process with high accuracy.
The metal sheet is bent into the required shape for assembly. Proper bending ensures structural strength and durability. This step helps in achieving the desired solar heater shape.
The sheet edges are welded together using a linear welding fixture. This ensures strong and seamless joints. Proper welding prevents leakage and increases durability.
Embossing adds patterns or reinforcements to the metal sheet. It improves the overall strength and aesthetic appeal. This step enhances the sheet’s resistance to deformation.
Both End Edge Bending
The edges of the sheet are bent on both sides for assembly. This ensures a secure fit and proper alignment of components. Edge bending improves structural stability.
Learn More
The hydraulic press shapes the metal cover with precision. High pressure ensures uniform thickness and durability. This step is essential for achieving a leak-proof cover.
Circular components are cut out for the solar heater body. Precise cutting ensures proper assembly and fitment. This step reduces material wastage and improves efficiency.
The edges of the cover are trimmed and steps are formed. Trimming ensures smooth and even edges for perfect sealing. This step enhances the overall fit and finish of the cover.
Cover Nipple Welding Fixture
Nipples are welded onto the cover to allow fluid flow. Proper welding ensures leak-proof connections. This step is crucial for the heater’s efficiency and functionality.
Learn More
The cylindrical tank body is welded together in a round formation. Strong welding ensures durability and prevents leakage. This step is essential for forming the main tank structure.
Holes are precisely cut and punched for fittings and connections. Accurate hole placement ensures proper assembly of parts. This step enhances the efficiency of the solar heater system.
The edges of the sheet are folded to strengthen the structure. Proper folding ensures better fitment and durability. This step prevents sharp edges and improves safety.
Edge Locking Machine
The folded edges are locked together to secure the structure. This process ensures a firm and leak-proof joint. Proper locking enhances the longevity of the solar heater.
Learn More
Grooves and nurls are added to the metal surface for reinforcement. This process improves grip and structural strength. Proper grooving enhances the overall stability of the tank.
Hole Cutting & Punching Machine
Additional holes are cut and punched for assembly. Precise holes allow easy installation of accessories. This step ensures proper functionality of the solar heater.
Learn More
Solar Heater Production Plant
The final assembled solar heater is ready for installation. All components are securely fitted for efficient performance. The finished product undergoes quality checks before dispatch.