SS Milk Machinery Plant From Start to Finish
We follow a streamlined and precise process to manufacture high-quality canisters that meet global standards. Each step in our process is designed to ensure durability, efficiency, and superior craftsmanship.
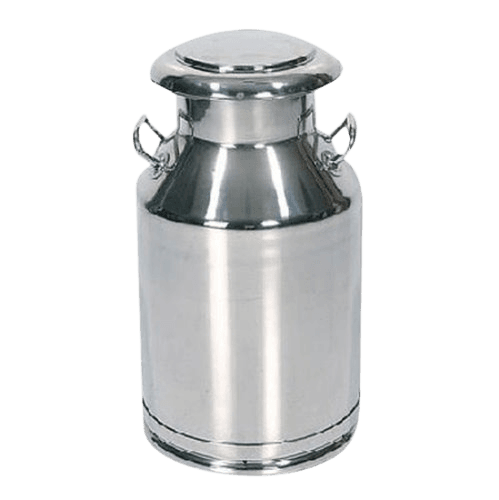

The stainless steel sheet is carefully cut to the required size. This step ensures precision in material dimensions for the next process. Proper cutting is essential to maintain uniformity and minimize wastage.
Circle Cutting Machine
Circular pieces are cut out from the sheet metal for the can’s base and lid. This step ensures that the components have accurate measurements. A smooth and precise cut is necessary for seamless assembly.
Learn More
The pre-cut sheet is pressed into a cylindrical shape to form the can body. This process provides the basic structure for the milk can. High pressure is used to achieve a uniform and strong form.
A hole is precisely cut at the top section of the can to create the neck opening. This ensures the proper fitment of the lid and allows easy pouring. Accuracy in cutting is vital for a leak-proof design.
The rough edges of the sheet are trimmed to achieve a smooth finish. Removing sharp edges is essential for safety and ease of handling. This step also ensures proper alignment for the welding process.
The cylindrical structure undergoes further shaping and reinforcement. This process enhances the strength and stability of the milk can. It ensures the can maintains its shape even under external pressure.
Trimming Machine
Excess material is cut off to achieve precise dimensions and symmetry. This step ensures that all components fit together seamlessly. A well-trimmed can body improves the overall look and function.
Learn More
Grooves or beads are formed along the body to add strength and durability. These reinforcements prevent deformation during usage. Beading also enhances the visual appeal of the milk can.
The cylindrical body is welded together using precision techniques. Strong and seamless welding ensures leak-proof joints. Proper welding enhances the longevity of the milk can.
The welded body undergoes a finishing process to refine its round shape. This ensures smooth edges and proper alignment with other components. A well-finished can body is easier to handle and assemble.
Hydraulic Die Cushion Press For Lid
The lid is shaped and pressed to ensure a tight and secure fit. This helps in maintaining an airtight seal when the lid is closed. A well-pressed lid enhances the overall usability of the milk can.
Learn More
The lid is welded securely to maintain structural integrity. A properly welded lid ensures that it remains durable and resistant to leaks. This step enhances the milk can’s longevity and usability.
A reinforcing ring is bent and shaped to add strength to the can. This step prevents deformation and improves impact resistance. A well-bent ring enhances the can’s durability during rough handling.
The reinforcing ring is welded onto the body for additional support. This ensures that the can remains sturdy and well-balanced. A firmly attached ring enhances the milk can’s structural stability.
Hydraulic Got Mahcine For Bottom Ring
The base of the milk can is shaped and pressed to provide stability. A strong and evenly formed base prevents tipping and wobbling. This ensures durability and reliability for long-term use.
Learn More
Handles and bottom reinforcements are securely attached for easy handling. This step ensures that the can is convenient to carry and transport. Proper attachment enhances user comfort and safety.
Pressing Dies For Press
Handles larger containers, providing hydraulic force to create consistent forms. Ensures reliability and precision for heavy-duty container production.
Learn More
Hydraulic Deep Draw Press
Performs deep drawing operations to create the container’s depth and body. Handles complex shapes while maintaining material integrity.
Learn More
Polish Motor
The milk can undergoes a final polishing process for a smooth and shiny finish. This enhances its visual appeal and prevents surface corrosion. A well-polished can looks professional and is easier to clean.